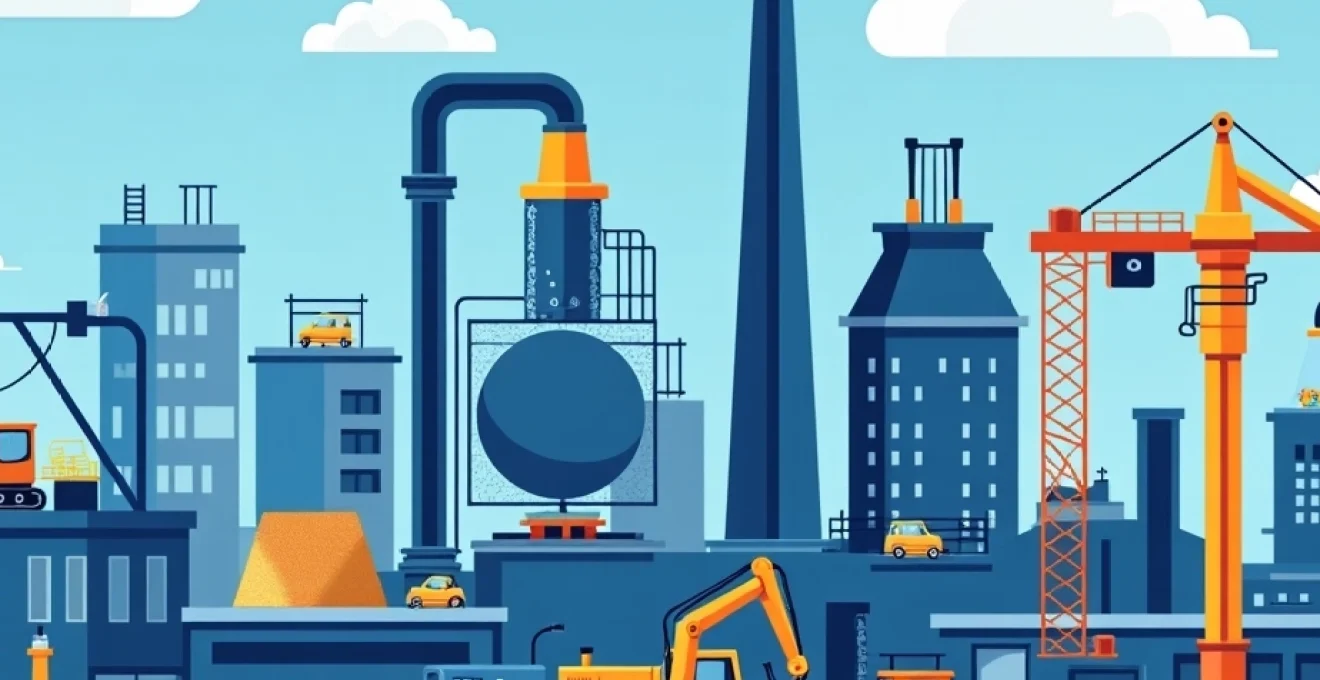
L'industrie moderne évolue rapidement, adoptant des technologies de pointe pour optimiser ses processus et améliorer sa productivité. Les outils de production, véritables piliers de cette transformation, jouent un rôle crucial dans la compétitivité des entreprises. De l'automatisation avancée à la fabrication additive, en passant par les logiciels de gestion intégrée, ces outils redéfinissent les paradigmes de la production industrielle. Mais comment ces technologies s'intègrent-elles concrètement dans les usines d'aujourd'hui ? Quels avantages apportent-elles aux fabricants ? Explorons ensemble le paysage fascinant des outils de production modernes et leur impact sur l'industrie 4.0.
Chaînes de production automatisées : systèmes et technologies
L'automatisation des chaînes de production représente l'un des piliers de l'industrie moderne. Elle permet d'optimiser les processus, de réduire les erreurs et d'augmenter significativement la productivité. Les systèmes et technologies qui sous-tendent cette automatisation sont en constante évolution, offrant des possibilités toujours plus avancées aux industriels.
Automates programmables industriels (API) : piliers de l'automatisation
Les automates programmables industriels (API) constituent le cœur des systèmes d'automatisation. Ces ordinateurs robustes, conçus pour résister aux environnements industriels difficiles, contrôlent et supervisent les processus de production. Ils interprètent les signaux provenant de capteurs, exécutent des programmes logiques complexes et commandent divers actionneurs pour assurer le bon fonctionnement des machines.
L'utilisation des API offre une flexibilité incomparable aux industriels. En effet, ces dispositifs peuvent être reprogrammés rapidement pour s'adapter aux changements de production ou à l'introduction de nouveaux produits. De plus, leur capacité à communiquer avec d'autres systèmes les rend essentiels dans la mise en place de l'usine connectée.
Systèmes SCADA : supervision et contrôle des processus
Les systèmes SCADA ( Supervisory Control And Data Acquisition ) représentent un maillon essentiel dans la chaîne de contrôle et de supervision des processus industriels. Ces logiciels sophistiqués permettent de collecter, d'analyser et de visualiser en temps réel les données provenant des différents équipements de production.
Grâce aux interfaces graphiques intuitives des systèmes SCADA, les opérateurs peuvent surveiller l'ensemble du processus de fabrication, détecter rapidement les anomalies et intervenir à distance si nécessaire. Cette centralisation de l'information améliore considérablement la réactivité et l'efficacité des équipes de production.
Robots industriels : intégration et programmation avancée
Les robots industriels ont révolutionné de nombreux secteurs de la production. Ces machines polyvalentes peuvent effectuer des tâches répétitives avec une précision et une endurance inégalées. L'intégration de robots dans les chaînes de production permet non seulement d'augmenter la cadence de fabrication, mais aussi d'améliorer la qualité des produits en éliminant les erreurs humaines.
La programmation avancée des robots industriels ouvre de nouvelles perspectives. Les cobots (robots collaboratifs) peuvent désormais travailler en toute sécurité aux côtés des opérateurs humains, combinant la force et la précision de la machine avec la flexibilité et l'intelligence humaine. Cette symbiose homme-machine représente l'avenir de nombreux processus de production.
Internet industriel des objets (IIoT) : connectivité et analyse en temps réel
L'Internet industriel des objets (IIoT) marque une étape cruciale dans l'évolution des outils de production. Cette technologie permet de connecter l'ensemble des équipements, capteurs et systèmes d'une usine à un réseau centralisé. Les données collectées en temps réel offrent une visibilité sans précédent sur l'ensemble du processus de production.
L'analyse de ces données massives ( Big Data ) permet d'optimiser les processus, de prédire les pannes avant qu'elles ne surviennent et d'adapter la production en fonction de la demande. L'IIoT est ainsi le fer de lance de l'usine intelligente, capable de s'auto-optimiser et de s'adapter rapidement aux changements du marché.
Outils de conception et simulation pour l'industrie 4.0
Dans l'ère de l'industrie 4.0, la conception et la simulation jouent un rôle prépondérant dans l'optimisation des processus de production. Ces outils permettent aux ingénieurs de concevoir, tester et affiner virtuellement leurs produits et processus avant même la phase de prototypage physique, réduisant ainsi considérablement les coûts et les délais de mise sur le marché.
CAO/FAO : de SolidWorks à CATIA pour l'optimisation des designs
Les logiciels de Conception Assistée par Ordinateur (CAO) et de Fabrication Assistée par Ordinateur (FAO) sont devenus indispensables dans le processus de développement de produits. Des outils comme SolidWorks, largement utilisé dans les PME, aux suites plus complètes comme CATIA, plébiscitée par les grands groupes industriels, ces logiciels offrent une palette d'outils puissants pour créer et optimiser des designs complexes.
La CAO permet de créer des modèles 3D détaillés, d'effectuer des analyses de résistance des matériaux et même de simuler l'assemblage virtuel des composants. La FAO, quant à elle, traduit ces modèles en instructions précises pour les machines de fabrication, assurant une transition fluide entre la conception et la production.
Simulation numérique : ansys et siemens NX pour les tests virtuels
La simulation numérique représente une avancée majeure dans le processus de développement de produits. Des logiciels comme Ansys et Siemens NX permettent de réaliser des tests virtuels poussés, simulant le comportement des produits dans diverses conditions d'utilisation. Ces outils sont particulièrement précieux dans des domaines comme l'aérospatiale ou l'automobile, où les tests physiques sont coûteux et complexes à mettre en œuvre.
Grâce à ces simulations, les ingénieurs peuvent :
- Optimiser les performances des produits avant la fabrication
- Identifier et résoudre les problèmes potentiels dès la phase de conception
- Réduire le nombre de prototypes physiques nécessaires
- Accélérer le processus de développement tout en améliorant la qualité finale
Jumeaux numériques : création et utilisation dans la production
Le concept de jumeau numérique représente l'une des innovations les plus prometteuses de l'industrie 4.0. Il s'agit d'une réplique virtuelle exacte d'un produit, d'un processus ou d'un système complet, mise à jour en temps réel grâce aux données collectées par des capteurs IoT.
L'utilisation de jumeaux numériques dans la production offre de nombreux avantages :
- Surveillance en temps réel des performances des équipements
- Prédiction des pannes et optimisation de la maintenance
- Test virtuel de modifications ou d'améliorations avant leur mise en œuvre physique
- Optimisation continue des processus de production
Les jumeaux numériques représentent l'avenir de la gestion des actifs industriels, permettant une compréhension sans précédent de leur comportement et de leurs performances tout au long de leur cycle de vie.
Équipements de fabrication additive et usinage CNC
La fabrication additive, communément appelée impression 3D, et l'usinage CNC (Commande Numérique par Calculateur) sont deux technologies complémentaires qui révolutionnent les méthodes de production traditionnelles. Ces équipements offrent une flexibilité et une précision inégalées, permettant la création de pièces complexes impossibles à réaliser avec les méthodes conventionnelles.
L'impression 3D, en particulier, a connu un essor fulgurant ces dernières années. Cette technologie permet de créer des objets en ajoutant de la matière couche par couche, offrant ainsi une liberté de conception presque illimitée. De la production de prototypes rapides à la fabrication de pièces finales en petites séries, l'impression 3D trouve des applications dans de nombreux secteurs industriels.
L'usinage CNC, quant à lui, reste incontournable pour la production de pièces métalliques de haute précision. Les machines-outils à commande numérique peuvent réaliser des opérations complexes de fraisage, tournage ou perçage avec une précision micrométrique. L'intégration de technologies comme la fabrication hybride , combinant impression 3D et usinage CNC, ouvre de nouvelles perspectives pour la production de pièces aux géométries complexes avec des finitions de haute qualité.
Logiciels MES et ERP pour la gestion de production
La gestion efficace de la production repose aujourd'hui sur des systèmes logiciels intégrés capables de centraliser et d'analyser l'ensemble des données de l'entreprise. Les systèmes MES (Manufacturing Execution System) et ERP (Enterprise Resource Planning) jouent un rôle crucial dans l'optimisation des processus de production et la prise de décision éclairée.
SAP S/4HANA : planification intégrée des ressources
SAP S/4HANA représente l'évolution la plus avancée des systèmes ERP proposés par le géant allemand SAP. Cette suite logicielle intègre l'ensemble des fonctions de gestion de l'entreprise, de la finance à la production en passant par les ressources humaines et la supply chain. Grâce à sa base de données in-memory, SAP S/4HANA offre des performances de traitement exceptionnelles, permettant des analyses en temps réel et une prise de décision plus rapide.
Pour les industriels, SAP S/4HANA apporte une visibilité globale sur l'ensemble de la chaîne de valeur. La planification de la production peut ainsi être optimisée en tenant compte de l'ensemble des contraintes de l'entreprise, des prévisions de ventes aux capacités de production en passant par la disponibilité des matières premières.
Odoo manufacturing : solution open-source pour PME
Odoo Manufacturing se positionne comme une alternative open-source attractive pour les PME industrielles. Ce module, intégré à la suite Odoo ERP, offre un ensemble complet de fonctionnalités pour gérer l'ensemble du processus de production, de la planification à la qualité en passant par la maintenance des équipements.
Les avantages d'Odoo Manufacturing incluent :
- Une interface utilisateur intuitive et personnalisable
- Une intégration native avec les autres modules Odoo (ventes, achats, comptabilité...)
- Des coûts de mise en œuvre et de maintenance réduits grâce à son modèle open-source
- Une grande flexibilité permettant d'adapter le logiciel aux spécificités de chaque entreprise
Microsoft dynamics 365 : suite complète pour l'industrie
Microsoft Dynamics 365 propose une suite complète d'applications cloud pour la gestion d'entreprise, incluant des modules spécifiques pour l'industrie manufacturière. Cette solution se distingue par son intégration poussée avec l'écosystème Microsoft, notamment Office 365 et Power BI pour l'analyse de données.
Pour les industriels, Dynamics 365 offre des fonctionnalités avancées telles que :
- La planification de la production basée sur l'IA
- La gestion des actifs et de la maintenance prédictive
- L'optimisation de la chaîne d'approvisionnement
- Des tableaux de bord personnalisables pour le suivi en temps réel des KPI de production
L'intégration d'un ERP moderne comme Dynamics 365 permet aux industriels de gagner en agilité et en compétitivité, en s'appuyant sur des données fiables et actualisées pour piloter leur activité.
Outils de maintenance prédictive et GMAO
La maintenance des équipements industriels a connu une véritable révolution avec l'avènement de la maintenance prédictive et des outils de Gestion de Maintenance Assistée par Ordinateur (GMAO). Ces technologies permettent non seulement d'optimiser les coûts de maintenance, mais aussi d'améliorer significativement la disponibilité des équipements, un facteur clé de la performance industrielle.
Capteurs IoT et analyse vibratoire pour la détection précoce
L'utilisation de capteurs IoT pour la surveillance en continu des équipements industriels représente une avancée majeure dans le domaine de la maintenance prédictive. Ces capteurs, connectés à des systèmes d'analyse avancés, permettent de détecter les signes précoces de défaillance bien avant qu'une panne ne survienne.
L'analyse vibratoire, en particulier, s'est imposée comme une technique incontournable pour la surveillance des machines tournantes. En analysant les profils vibratoires des équipements, il est possible de détecter avec précision :
- Les désalignements
- Les déséquilibres
- L'usure des roulements
- Les problèmes de lubrification
Ces informations permettent aux équipes de maintenance d'intervenir de manière ciblée et proactive, réduisant ainsi les temps d'arrêt imprévus et prolongeant la durée de vie des équipements.
Logiciels GMAO : de CARL source à IBM maximo
Les logiciels de GMAO jouent un rôle central dans la gestion efficace de la maintenance industrielle. Des solutions comme CARL Source, particulièrement populaire en Europe, ou IBM Maximo, reconnu mondialement, offrent un ensemble complet de fonctionnalités pour planifier, exécuter et suivre les opérations de maintenance.
Ces outils permettent notamment :
- La gestion détaillée des actifs industriels
- La planification et le suivi des interventions de maintenance
- La gestion des stocks de pièces détachées
- L'analyse des coûts et des indicateurs de performance de maintenance
- La gestion documentaire (plans, procédures, historiques)
L'intégration de ces outils GMAO avec les systèmes de capteurs IoT et d'analyse prédictive permet de passer d'une maintenance réactive ou préventive systématique à une maintenance véritablement prédictive, optimisant ainsi les ressources et minimisant les temps d'arrêt.
Intelligence artificielle dans la prédiction des pannes
L'intelligence artificielle (IA) et le machine learning apportent une dimension supplémentaire à la maintenance prédictive. En analysant de vastes ensembles de données historiques et en temps réel, les algorithmes d'IA peuvent identifier des schémas complexes annonciateurs de pannes, souvent imperceptibles pour l'œil humain.
Les applications de l'IA dans la prédiction des pannes incluent :
- L'analyse prédictive basée sur des modèles statistiques avancés
- La détection d'anomalies en temps réel
- L'optimisation des intervalles de maintenance en fonction de l'utilisation réelle des équipements
- La recommandation automatisée d'actions de maintenance préventive
Grâce à ces technologies, les industriels peuvent non seulement anticiper les pannes, mais aussi comprendre leurs causes profondes et optimiser continuellement leurs processus de maintenance.
L'intégration de l'IA dans les stratégies de maintenance prédictive permet aux entreprises de réduire jusqu'à 50% leurs coûts de maintenance tout en augmentant la disponibilité des équipements.
Sécurité et conformité : outils pour l'industrie moderne
Dans un environnement industriel de plus en plus complexe et réglementé, la gestion de la sécurité et de la conformité devient un enjeu crucial. Les outils modernes permettent non seulement de garantir la sécurité des opérateurs et des installations, mais aussi d'assurer la conformité avec les normes et réglementations en vigueur.
Parmi les solutions clés dans ce domaine, on peut citer :
- Les systèmes de gestion de la sécurité (SGS) intégrés
- Les logiciels de suivi et de reporting des incidents
- Les plateformes de formation en réalité virtuelle pour la sécurité
- Les outils d'audit et de gestion de la conformité réglementaire
Ces outils permettent aux industriels de mettre en place une culture de sécurité proactive, de réduire les risques d'accidents et de démontrer leur conformité aux autorités de régulation.
L'utilisation de technologies comme l'IoT et l'IA dans ce domaine ouvre également de nouvelles perspectives. Par exemple, des capteurs connectés peuvent surveiller en temps réel les niveaux de gaz dangereux ou les paramètres environnementaux critiques, déclenchant des alertes immédiates en cas de dépassement des seuils de sécurité.
En matière de conformité, les logiciels spécialisés permettent de centraliser la gestion documentaire, de suivre les évolutions réglementaires et d'automatiser la génération de rapports de conformité. Cela simplifie considérablement les processus d'audit et réduit les risques de non-conformité.
Investir dans des outils modernes de sécurité et de conformité n'est pas seulement une obligation réglementaire, c'est aussi un moyen d'améliorer la performance globale de l'entreprise en réduisant les risques et en renforçant la confiance des parties prenantes.
En conclusion, les outils de production modernes offrent aux industriels des moyens sans précédent pour optimiser leurs processus, améliorer leur productivité et renforcer leur compétitivité. De l'automatisation avancée à la maintenance prédictive, en passant par la conception assistée par ordinateur et la gestion intégrée de la production, ces technologies redéfinissent les standards de l'industrie 4.0. Cependant, leur adoption réussie nécessite une approche stratégique, une formation adéquate des équipes et une culture d'entreprise ouverte à l'innovation continue. Les entreprises qui sauront tirer parti de ces outils et les intégrer efficacement dans leur écosystème seront les mieux positionnées pour relever les défis de l'industrie du futur.